Precision Injection Molds: A Deep Dive into the Manufacturing Marvel
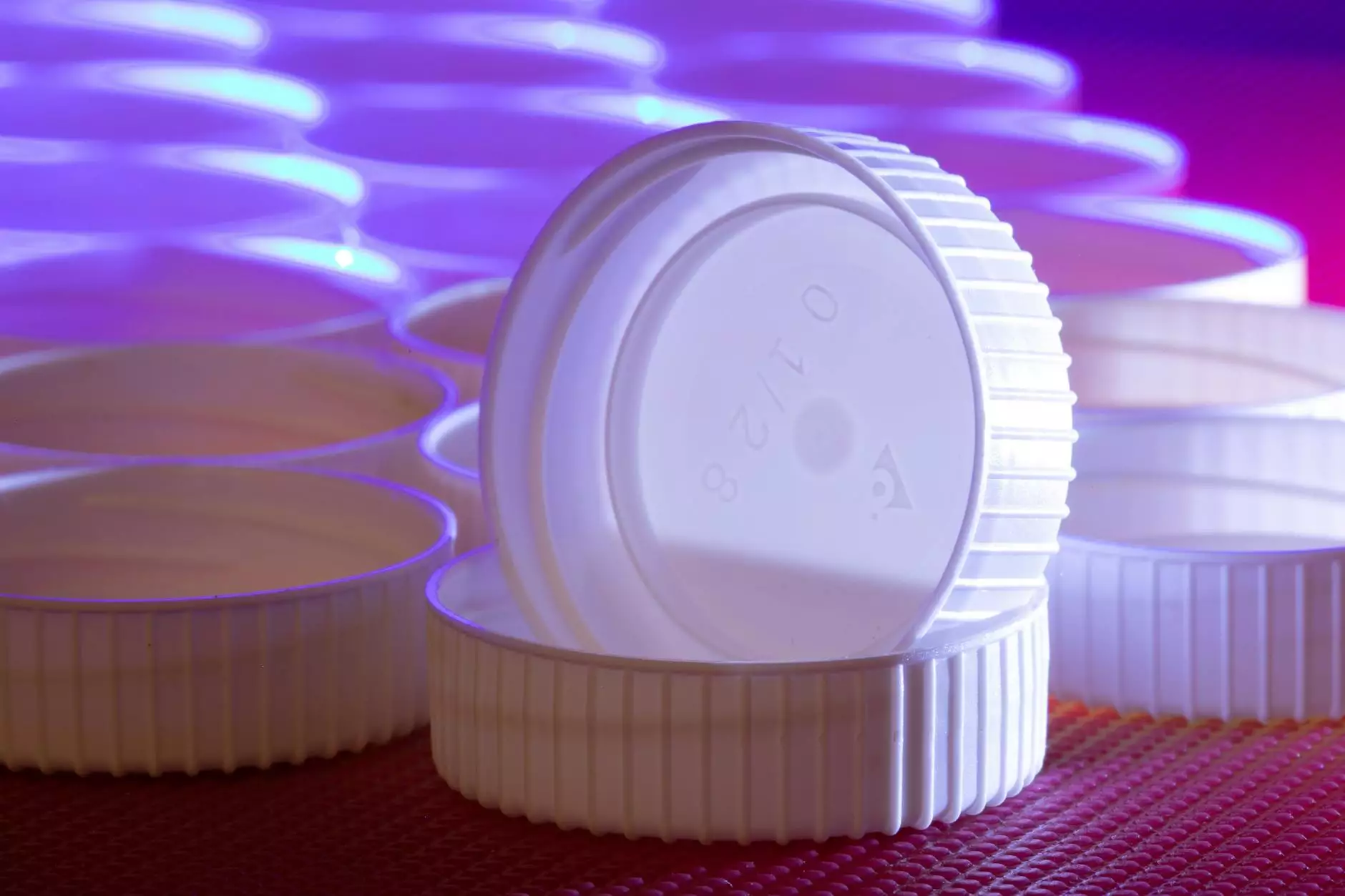
In the realm of modern manufacturing, precision injection molds stand out as a cornerstone of efficient production processes. These molds facilitate the creation of complex shapes in high volumes, making them indispensable for industries ranging from automotive to consumer goods. In this comprehensive article, we will explore the essence of precision injection molds, examining their design, functionality, and the significant impact they have on the manufacturing sector.
What are Precision Injection Molds?
Precision injection molds are specialized tools used to produce parts by injecting molten material into a mold cavity. The process involves several crucial steps:
- Material Preparation: The raw material, usually thermoplastics, is prepared and heated until it becomes pliable.
- Injection: The molten material is injected into the mold under high pressure.
- Cooling: Once filled, the mold is cooled to solidify the material into the desired shape.
- Demolding: The finished part is ejected from the mold.
This technique enables manufacturers to produce high-quality and consistent components with intricate details, which are often unattainable through other manufacturing processes. The precision and repeatability of the injection molding process make it particularly valuable in large-scale production.
The Importance of Precision in Injection Molding
Precision is not merely a feature; it is a requirement in precision injection molds. Accurate mold design and manufacturing can significantly impact product performance and production efficiency. Here are several reasons why precision is critical:
- Quality Assurance: High precision reduces defects and variability. Components that meet stringent specifications enhance end-product quality.
- Cost Efficiency: By minimizing waste and optimizing production time, precise molds can lead to significant cost savings over time.
- Flexibility in Design: Precision molds allow for complex geometries and designs, giving manufacturers the ability to innovate without sacrificing performance.
- Reputation and Reliability: Consistency in quality builds trust with clients, contributing to long-term business relationships.
Applications of Precision Injection Molds
From consumer products to industrial components, precision injection molds serve a wide array of applications:
1. Automotive Industry
The automotive sector relies heavily on precision injection molds for parts such as dashboards, panels, and components that require high precision to fit perfectly in assembly. These molds contribute to the overall safety and efficiency of vehicles.
2. Electronics
In the electronics industry, precision is vital. Molds manufacture cases, connectors, and internal components that need to meet strict dimensional tolerances and enhance functionality.
3. Medical Devices
The medical field demands the highest levels of precision and hygiene. Injection molds are used to create components for devices, surgical instruments, and packaging that adhere to stringent regulatory standards.
4. Consumer Goods
Everyday items such as kitchenware, toys, and household products utilize precision injection molds to achieve the desired aesthetics and functionality at a low production cost.
Factors Influencing the Quality of Precision Injection Molds
Several elements impact the quality and effectiveness of precision injection molds:
- Material Selection: The choice of material for both the mold and the product significantly influences durability and precision. Common materials include steel, aluminum, and composite materials.
- Mold Design: A well-thought-out design that accounts for material flow, cooling channels, and ejection mechanisms is crucial for optimal performance.
- Manufacturing Process: Advanced machining techniques, such as Electrical Discharge Machining (EDM) and Computer Numerical Control (CNC) milling, enhance precision during mold fabrication.
- Maintenance: Regular upkeep of molds ensures longevity and consistent performance over time.
The Process of Creating Precision Injection Molds
The journey of creating precision injection molds involves several stages, each requiring meticulous attention to detail:
1. Concept and Design
The initial phase begins with understanding the product requirements. Designers use Computer-Aided Design (CAD) software to create detailed mold designs that account for the dimensions, cooling channels, and any necessary ejector systems.
2. Prototyping
Before constructing the actual mold, a prototype is often created to evaluate the design's form and function. This step helps identify potential issues early in the process.
3. Machining
Using precision machining techniques, the mold components are fabricated. This phase requires skilled labor and advanced machinery to ensure tight tolerances and surface finishes.
4. Assembly
After machining, the various components of the mold are assembled. This step includes installing moving parts and aligning the mold halves to ensure a proper fit.
5. Testing
Before full-scale production, the mold undergoes rigorous testing to evaluate its performance under operational conditions. This may include trial runs to produce sample parts, assessing cycle times, cooling effectiveness, and overall functionality.
Challenges Faced in Precision Injection Mold Manufacturing
Despite the advantages of precision injection molding, several challenges can hinder the process:
- Complex Designs: As products become more intricate, mold design and manufacturing also become increasingly complicated, which can challenge traditional methods.
- Production Speed: Maintaining a balance between precision and production speed is crucial yet challenging. Higher precision may lead to longer cycle times.
- Material Limitations: Not all materials are suitable for specific applications, and some may yield inferior results when subjected to the injection process.
- Technology Adaptation: Keeping up with the latest advancements in manufacturing technology can be daunting but essential for maintaining competitive advantage.
Future Trends in Precision Injection Molding
The evolution of precision injection molding is marked by several trends that promise to transform the industry:
1. Increased Use of Automation
Automation and robotics are becoming increasingly integral to the injection molding process, improving both speed and accuracy while reducing human error.
2. Advanced Materials
With the continuous development of new materials, such as biodegradable plastics and composites, the capabilities of precision injection molds are expanding, allowing for more sustainable production practices.
3. 3D Printing Integration
3D printing technology is being integrated into the mold-making process, enabling rapid prototyping and the creation of complex shapes that were previously infeasible.
4. Enhanced Simulation Software
New simulation software tools allow for better analysis of the injection process, predicting potential issues before they arise and optimizing mold designs for efficiency and quality.
Conclusion: Embracing the Future of Precision Injection Molds
As industries continue to evolve, the demand for precision injection molds will only increase. By embracing advanced technologies, focusing on quality assurance, and adapting to changing market needs, companies can position themselves as leaders in this essential sector. DeepMould.net exemplifies these principles, offering high-quality mold fabrication and exceptional service tailored to the specific requirements of their clients. In a world where precision is paramount, trusting in the expertise of seasoned professionals is vital for ensuring product excellence and operational success.