The Critical Role of Cleanroom Production in Electronics and Medical Supplies
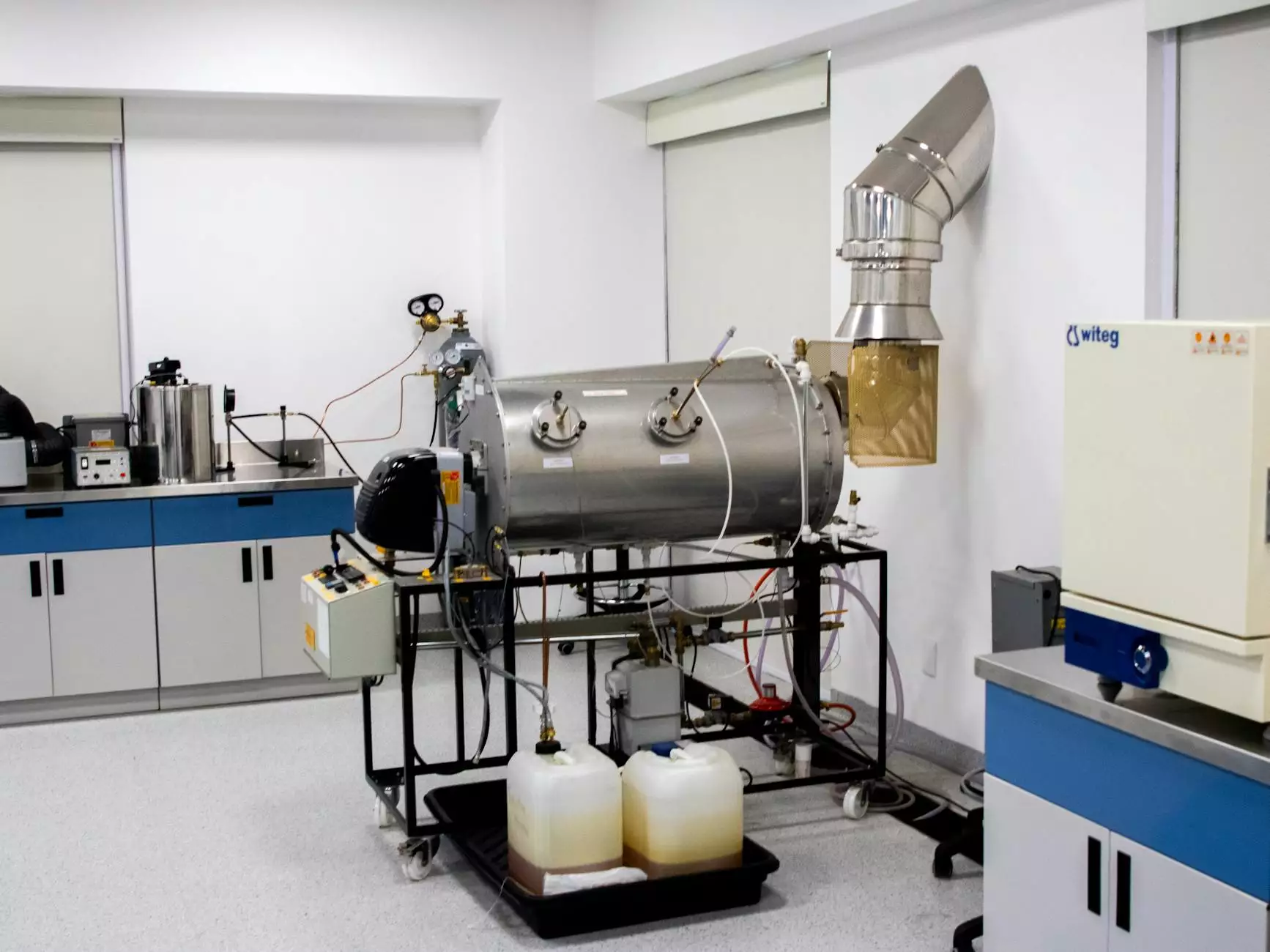
The world we live in today demands high-quality products across various industries, particularly in electronics and medical supplies. One of the foundational processes that ensure these products meet strict purity and quality standards is cleanroom production. In this comprehensive article, we will delve into what cleanroom production entails, its significance in electronics and medical supplies, and why understanding this process is essential for companies striving for excellence, such as Nolato.
What is Cleanroom Production?
Cleanroom production refers to the manufacturing and assembly processes conducted in controlled environments where the concentration of airborne particles is regulated. To achieve a cleanroom environment, several factors such as humidity, temperature, and airflow are meticulously managed. Cleanrooms are classified according to the number and size of particles allowed per volume of air, often categorized from ISO Class 1 (the cleanest) to ISO Class 9.
Why Does Cleanroom Production Matter?
In several industries, maintaining a contamination-free environment is critical. Cleanroom production plays a significant role in the following ways:
- Ensuring Product Integrity: Electronic components, such as semiconductors, can be severely affected by even the smallest particles. Cleanroom production helps in preventing defects that could compromise product performance.
- Compliance with Regulations: Industries like medical devices are subject to strict government regulations, ensuring that products are safe for human use. Cleanroom environments help companies comply with these regulations.
- Enhancing Product Quality: Products produced in cleanrooms usually exhibit fewer defects, which translates to higher reliability and satisfaction for consumers.
Applications of Cleanroom Production in Electronics
The electronics industry has significantly benefited from implementing cleanroom production processes. Here are some of the key applications:
1. Semiconductor Manufacturing
Semiconductors are essential for virtually all electronic devices. The manufacturing process involves several steps, including photolithography and etching, which are heavily impacted by environmental factors. Cleanrooms ensure that these processes occur without interference from airborne particles.
2. Printed Circuit Board (PCB) Assembly
The assembly of PCBs requires precision and cleanliness. Any contamination can lead to short circuits or other failures. By utilizing cleanroom production, manufacturers reduce the risk of defects, ensuring the reliability of electronic devices.
3. Device Packaging
Once electronic components are manufactured, packaging in a cleanroom environment prevents contamination from dust and other particles, safeguarding product integrity until it reaches the consumer.
Applications of Cleanroom Production in Medical Supplies
The medical sector is another realm where cleanroom production is indispensable. Here are some primary applications:
1. Medical Device Manufacturing
Medical devices, from surgical instruments to implants, must be produced in sterile environments to ensure patient safety. Cleanrooms allow for the production of these devices in adherence to regulatory standards.
2. Pharmaceutical Production
The production of drugs often requires cleanroom conditions to ensure that the final products are free of contaminants that could affect patient health. A cleanroom environment helps maintain the purity and efficacy of pharmaceutical products.
3. Laboratory Testing
Many laboratory tests are performed in cleanrooms to ensure that samples remain uncontaminated. This helps in obtaining accurate results, which are crucial for patient diagnoses and treatment plans.
Key Components of Cleanroom Production
To maintain a cleanroom environment, several critical components are necessary:
- HEPA Filters: High-Efficiency Particulate Air (HEPA) filters are crucial for removing particles from the air, ensuring a continuous flow of clean air.
- Controlled Temperature and Humidity: Properly controlling these factors helps in maintaining the integrity of products being manufactured.
- Positive Air Pressure: Cleanrooms generally operate with positive air pressure to prevent outside contaminants from entering the cleanroom area.
Challenges in Cleanroom Production
Although cleanroom production is vital, it does come with challenges:
1. Cost
Establishing and maintaining a cleanroom requires significant investment. From infrastructure to maintenance, the costs can be substantial, which may deter smaller companies from implementing such systems.
2. Training
Staff operating within cleanrooms must adhere to strict protocols. Training personnel effectively to follow these protocols is essential yet can be time-consuming and costly.
Strategies for Effective Cleanroom Management
To ensure that cleanroom production remains effective, companies can implement several strategies:
- Regular Monitoring: Continuous monitoring of particle counts and environmental conditions helps identify issues before they affect production.
- Employee Training: Regular training sessions and refreshers for staff can minimize contamination risks.
- Maintenance Programs: Scheduled maintenance of equipment and facilities ensures that cleanroom standards are consistently met.
Future Trends in Cleanroom Production
As technology advances, so does the field of cleanroom production. Some trends include:
1. Automation
Automation technologies are increasingly being employed to reduce human interaction within cleanrooms, minimizing the risk of contamination.
2. Real-Time Monitoring Systems
Real-time data analytics and IoT devices are making it easier to monitor cleanroom conditions continuously, providing instant feedback and fostering proactive management.
3. Modular Cleanrooms
The rise of modular cleanroom designs allows for flexibility and scalability in production, enabling companies to adapt to varying production needs without significant overhauls.
Conclusion
In conclusion, cleanroom production is essential for maintaining the integrity and quality of products in the electronics and medical supplies sectors. Companies like Nolato demonstrate the need for high-quality standards in their manufacturing processes to meet and exceed market expectations. As the industry evolves with advancements in technology and stricter regulations, cleanroom production will continue to play a pivotal role in ensuring that businesses can deliver exceptional products safely and reliably.