The Essential Guide to Plastic Injection Molds for Businesses
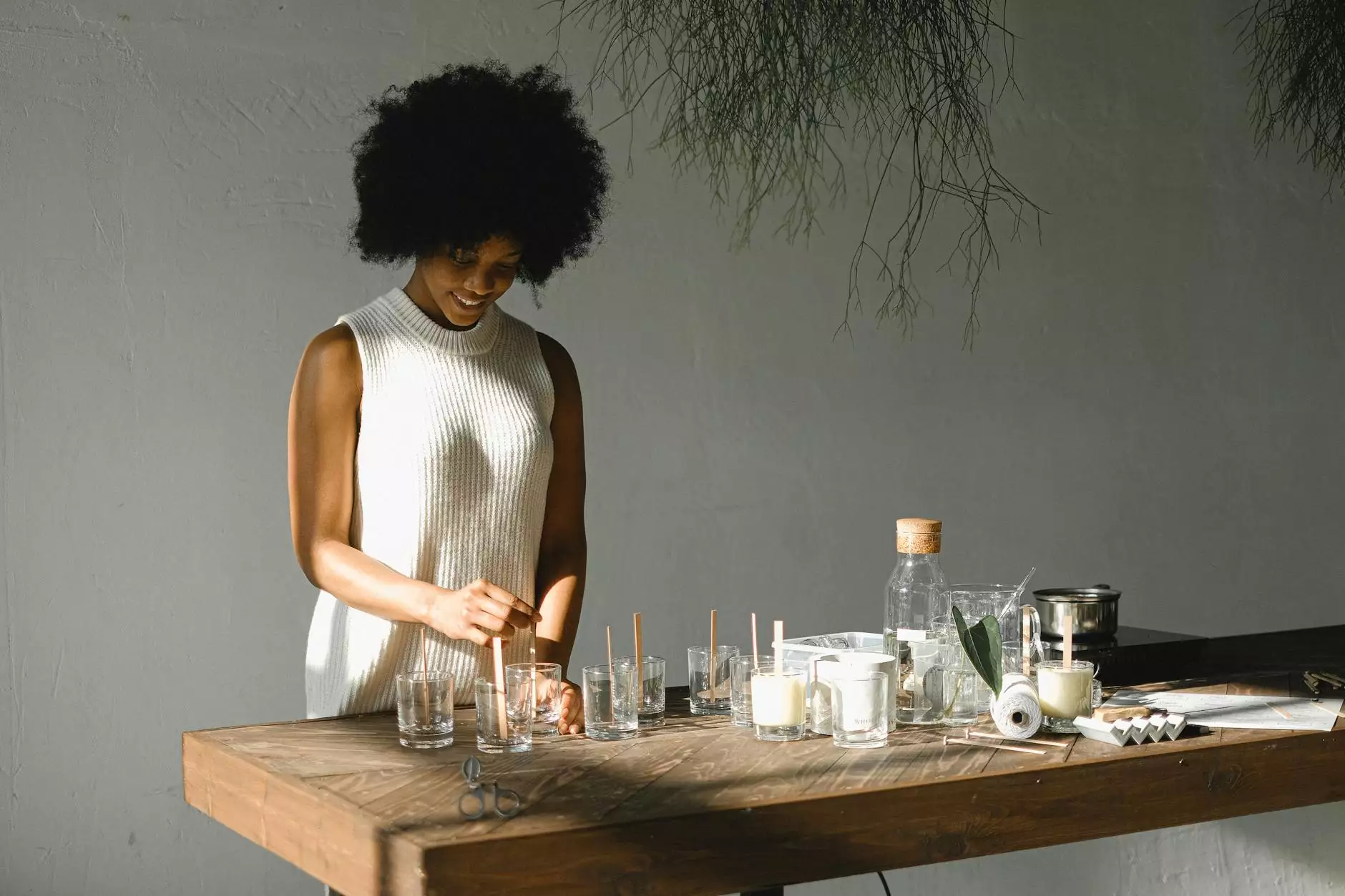
The world of manufacturing has undergone significant transformations over the years, leading to remarkable advancements in production techniques. Among these techniques, plastic injection molding stands out as a cornerstone of modern manufacturing, particularly for businesses involved in producing precise and intricate plastic components. This article delves into the key aspects of plastic injection molds, making it an invaluable resource for businesses looking to understand their importance and applications.
What is Plastic Injection Mold?
Plastic injection molding is a manufacturing process that involves injecting molten plastic into a mold to create various plastic parts. The process is known for its efficiency, precision, and ability to produce high-quality components in large volumes. Here’s a brief overview of how it works:
- Material Preparation: Raw plastic material, typically in the form of pellets, is heated until it becomes molten.
- Injection: The molten plastic is then injected under high pressure into a specially designed mold.
- Cooling: Once the mold is filled, the material cools down and solidifies into the shape of the desired part.
- Demolding: The mold is opened, and the newly formed plastic part is removed.
Benefits of Plastic Injection Molds
The adoption of plastic injection molds offers numerous advantages for businesses:
1. Cost-Effectiveness
One of the most significant benefits of plastic injection molding is its cost-effectiveness, especially for high-volume production. Once the initial mold has been created, the subsequent production runs are relatively inexpensive since the process can manufacture parts quickly and efficiently.
2. High Precision and Quality
Plastic injection molding provides exceptional precision, enabling manufacturers to produce parts with tight tolerances. This high level of accuracy reduces the need for secondary operations, thus enhancing the overall quality of the final product.
3. Versatility of Materials
Injection molding can accommodate a wide array of plastic materials, including thermoplastics and thermosetting plastics, allowing for customization based on specific application needs. This versatility expands the range of products that can be produced.
4. Speed of Production
The speed of the injection molding process is a significant advantage. The cycle time for creating a part can be as short as 15 to 30 seconds, allowing for rapid mass production.
5. Reduced Waste
Plastic injection molding generates less waste compared to traditional manufacturing processes. The design of molds allows for optimal utilization of materials, minimizing excess and scrap.
Applications of Plastic Injection Mold
Plastic injection molds are utilized across various industries and applications, showcasing their remarkable versatility. Here are some prominent areas where they play a vital role:
1. Automotive Industry
In the automotive sector, plastic injection molded parts are used extensively for manufacturing components such as dashboards, bumpers, and interior trim. The lightweight nature of plastic helps improve fuel efficiency without compromising safety.
2. Consumer Electronics
Smartphones, laptops, and other electronic devices rely heavily on precision-made plastic components for housing and various intricate internal parts. Injection molding ensures these components are lightweight, durable, and cost-effective.
3. Medical Devices
The medical industry benefits from injection molding in producing high-quality, sterile plastic parts for devices and instruments. Components such as surgical tools, casings for electronic medical devices, and disposables are often made using this process.
4. Packaging Solutions
Packaging plays a crucial role in product protection and branding, and injection-molded containers and closures are common in the food and beverage industry. This method allows for innovative designs that improve user convenience and product preservation.
5. Household Items
Everyday items such as toys, kitchenware, and storage solutions are often produced using plastic injection molding, thanks to its ability to create complex shapes and designs efficiently.
Choosing the Right Plastic Injection Mold Manufacturer
When selecting a manufacturer for your plastic injection mold needs, it is essential to consider several factors to ensure you are making an informed decision:
1. Experience and Expertise
Look for manufacturers that have substantial experience in the industry. A well-established company brings expertise and knowledge that can enhance your product development process.
2. Technology and Equipment
Evaluate the technology and equipment used by the manufacturer. Advanced machinery and up-to-date techniques can significantly improve production quality and speed.
3. Quality Assurance Processes
A reputable manufacturer should have a robust quality assurance process in place to ensure that every part meets the required specifications. Look for certifications and industry standards that indicate a commitment to quality.
4. Customer Service
Effective communication and customer service are critical. A manufacturer that prioritizes customer relationships can help you navigate challenges and ensure a smooth production process.
5. Cost Structures
While cost should not be the sole factor in your decision, it is important to understand the pricing structure and ensure it aligns with your budget without compromising on quality.
Innovations in Plastic Injection Molding
The field of plastic injection molding is continually evolving, with new technologies and innovations aimed at improving efficiency, sustainability, and production capabilities. Some of the latest advancements include:
1. 3D Printing and Rapid Prototyping
3D printing technologies are increasingly being integrated into the injection molding process. Rapid prototyping allows businesses to create and test molds quickly, reducing time-to-market and costs associated with traditional methods.
2. Biodegradable Plastics
As sustainability becomes a priority for many companies, the development of biodegradable plastics has emerged as a promising innovation. Injection molding can accommodate these materials, allowing for the production of environmentally friendly products.
3. Automation and Smart Factories
The rise of automation and the Internet of Things (IoT) in manufacturing has transformed injection molding operations. Automated processes enhance efficiency, reduce errors, and enable real-time monitoring and adjustments.
4. Enhanced Mold Design
Innovations in mold design, such as conformal cooling and multi-cavity molds, help improve efficiency and quality. These advancements lead to shorter cycle times and better thermal management during production.
Conclusion
In conclusion, plastic injection molds play a pivotal role in the modern manufacturing landscape. Their ability to produce high-quality, precise components quickly and cost-effectively makes them an indispensable tool for various industries. By understanding the benefits, applications, and ongoing innovations in this field, businesses can harness the full potential of injection molding to enhance their production processes and meet market demands.
For businesses looking to dive deeper into the world of plastic injection molding, partnering with a reliable manufacturer like DeepMould.net can provide the guidance and expertise needed to navigate the complexities of production while ensuring the highest quality outcomes.